Inspiration
The Power of Scour
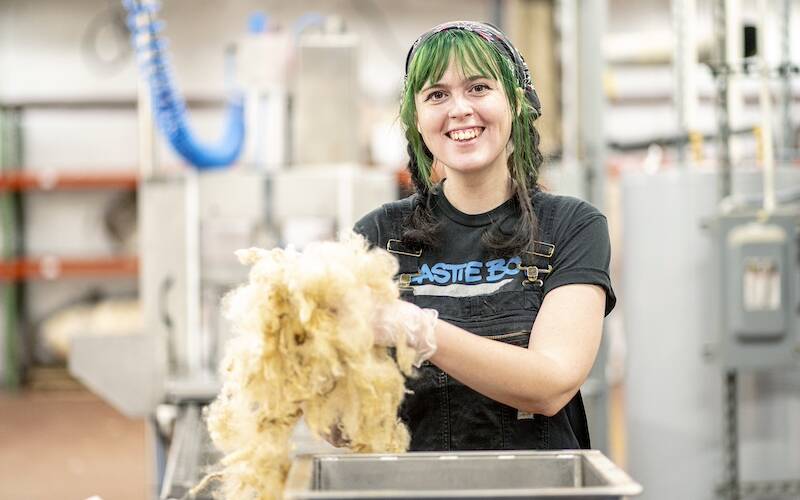
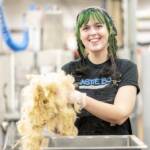
On a nondescript corner in the tiny upper Hudson Valley city of Mechanicville there’s a whole lot of washing going on. A sign on the side door of an industrial building covered with larger-than-life sports action art reads Clean Fleece. It’s a quiet entry into the farm-to-yarn cycle, a scouring facility opened in late 2023 by the Hudson Valley Textile Project.
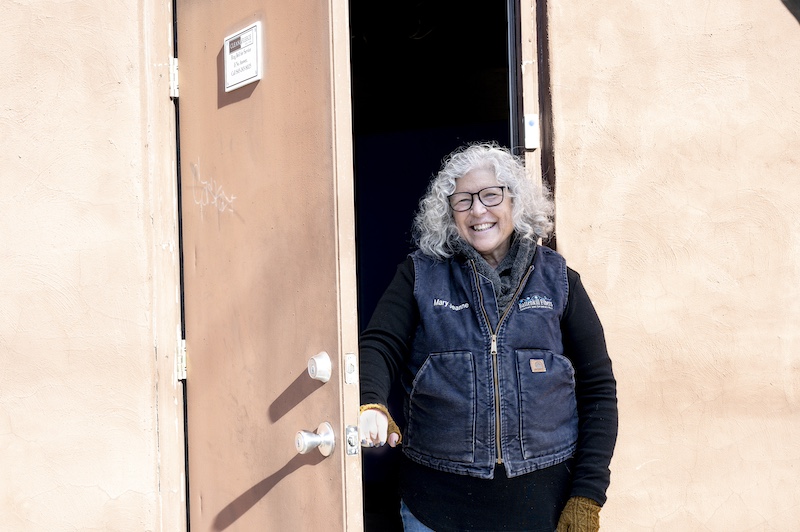
Mary Jeanne Packer, co-founder of the Hudson Valley Textile Project, the non-profit that owns Clean Fleece
Scouring is a necessary step in wool production. Sheep (and other fiber critters) live in fields and barns growing their coats. They’re sheared to remove their fleeces. Once shorn, the fleeces are skirted: picked over by hand to remove bits of plants, hay, and clumps of organic material. The fleeces are grease-covered and lanolin-redolent. The next step—whether the fleece is destined for yarn or felt or stuffing—is scouring: washing the wool in several baths of very hot water (180 degrees F) and pulling it apart to dry.
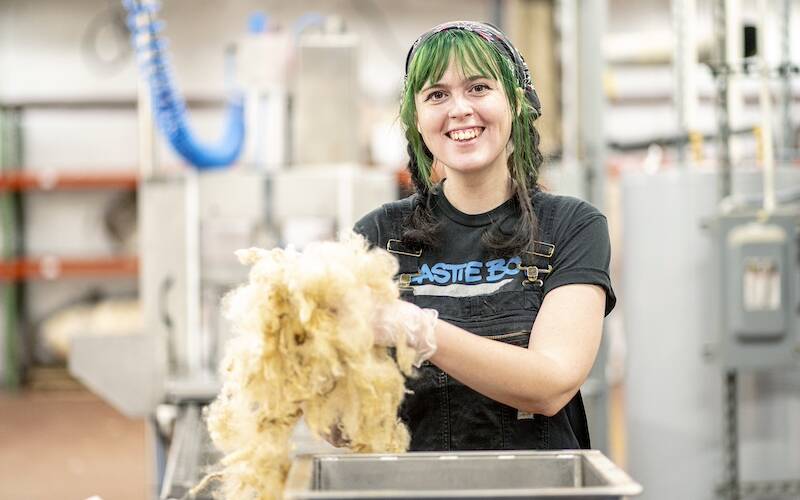
Norah Moses, Operations manager of Clean Fleece
The process is straightforward. At Clean Fleece, an automated Kiwi Scour machine moves the fleece in and out of a succession of baths in a perforated basket, from filthy to clean. The machine can’t agitate but it can compress and release. Finally, the clean, wet fleece is spread to dry.
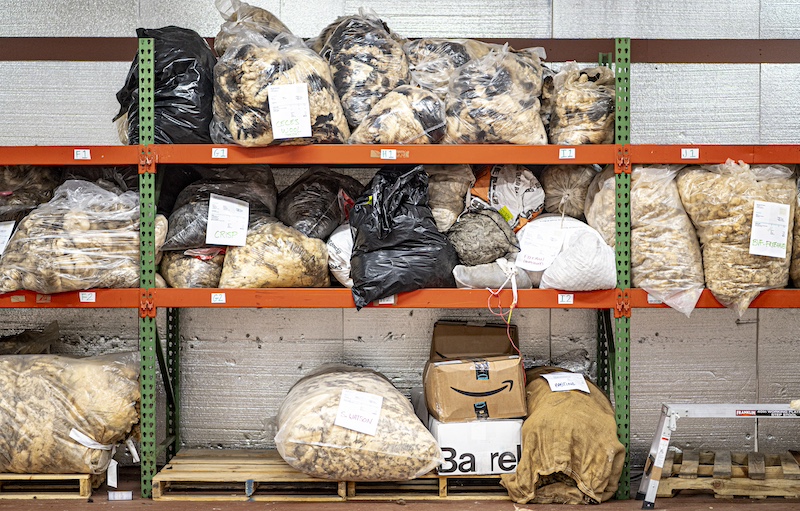
Fleeces waiting to be scoured. A minimum order is 50 pounds.
When Mary Jeanne Packer and Gail Parrinello put together a meet-up for a few dozen fiber folks in 2016, they had no idea they’d find themselves establishing a non-profit and then a scouring factory. Gail has sheep, makes yarn and felt, and owns Cornwall Yarn Shop in Cornwall, New York.
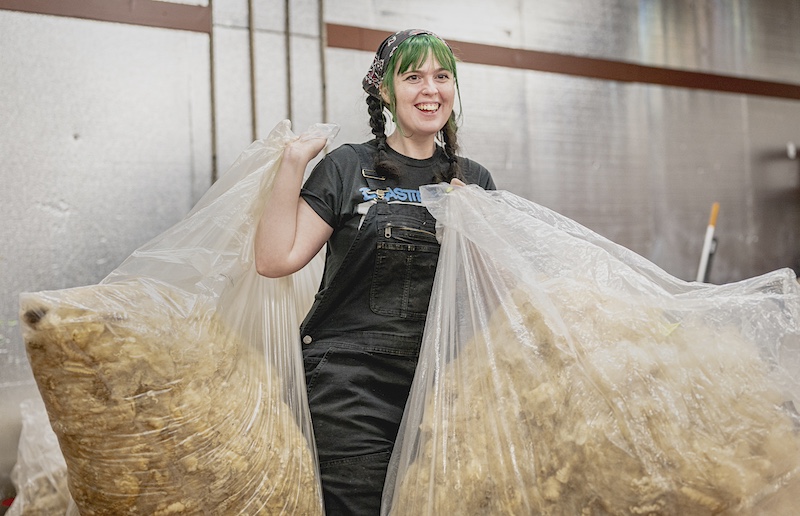
Norah with bags of greasy fleeces.
Further up the Hudson River Valley, Mary Jeanne Packer is the owner of Battenkill Fibers mill, spinning yarn from farms throughout the Hudson Valley and well beyond.
Their goal was networking for sheep and goat farmers, knitwear designers, shop owners, weavers, dyers, scientists, and anyone else in the region interested in fiber. If it went well, perhaps make it an annual event. From the conversation that first day, the need for a regional scouring facility stood out as the biggest challenge in the farm-to-fabric process.
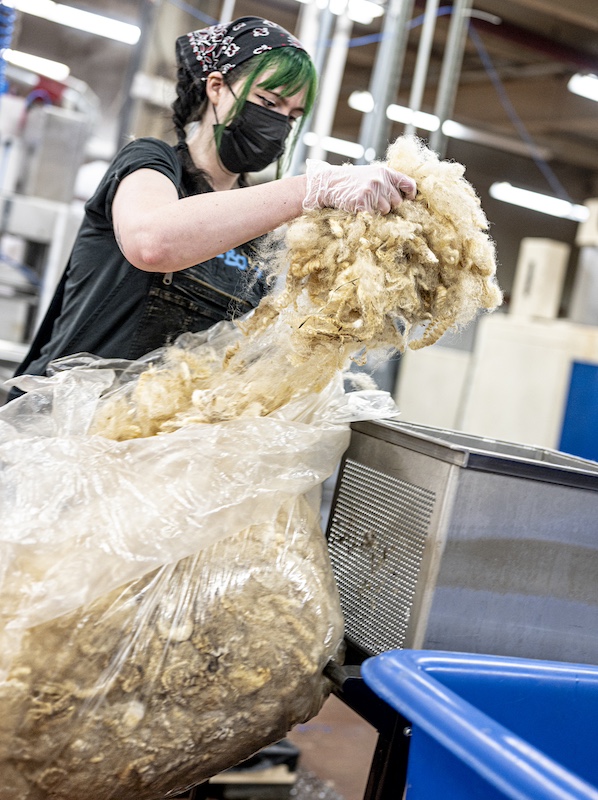
opening up greasy fleece and placing it into the bin for scouring.
Why? An average fleece is about five pounds. Most Hudson Valley farms are too small to ship the requisite 1000 pounds of (white only) fiber to a distant scouring house. Doing it themselves by hand is inefficient, and so is storing fleece year after year to accumulate a large enough batch to ship out. Locally, Mary Jeanne’s mill had a bottleneck of wool waiting for their modest scouring capabilities.
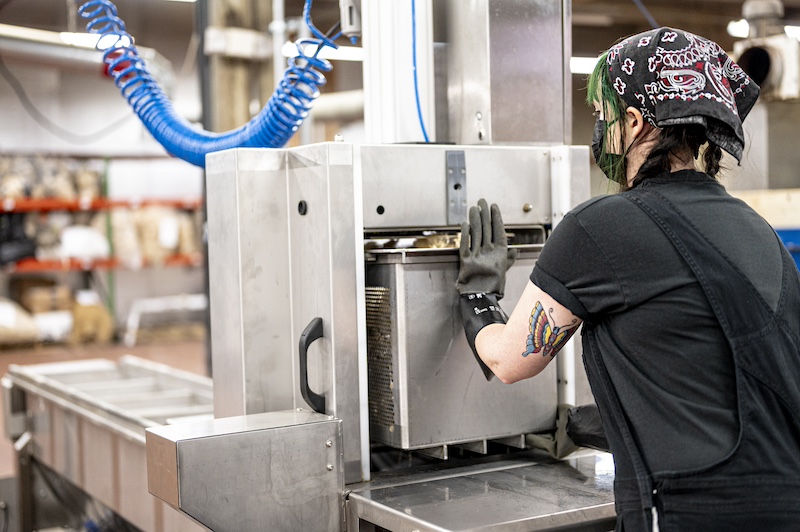
Loading the bin of fleece into the Kiwi Scour
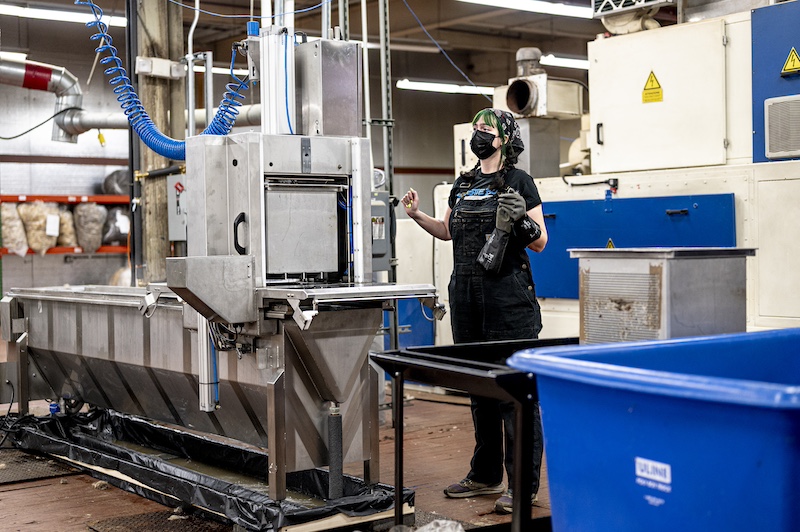
checking the control panels of the Kiwi Scour machine as the batch processed through three baths
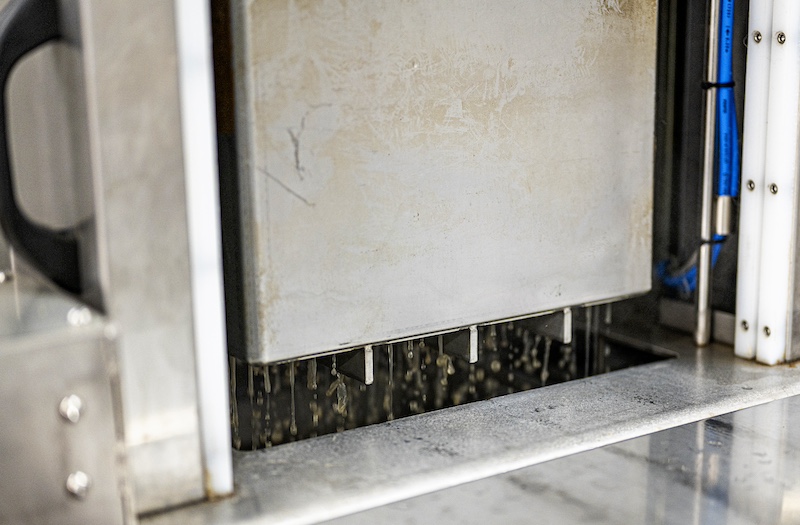
DirtY water rinsing out of the bin of fleece
A year after the gathering, the Hudson Valley Textile Project launched as a non-profit serving the interests of anyone in the fibershed from New York City to the lower Adirondacks. Five years later, Clean Fleece became a reality.
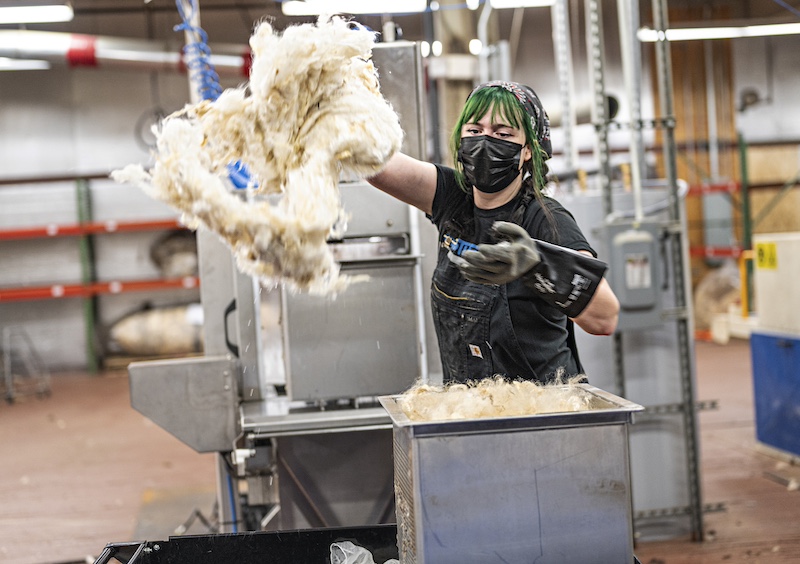
Norah throws batches of clean fleece from the bin to a rack nearby.
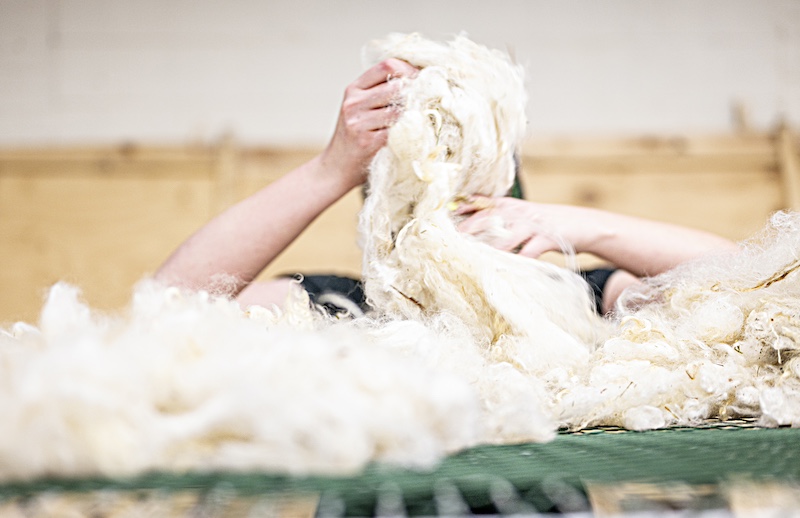
Clean fleece being spead apart to dry on racks.
Inside Clean Fleece, a green haired artist named Norah Moses (whose great great great was Grandma Moses, for real) is Operations Manager. She places 50-pound dirty fleece batches in for a wash, monitors the second wash, the third wash, and pulls them out clean.
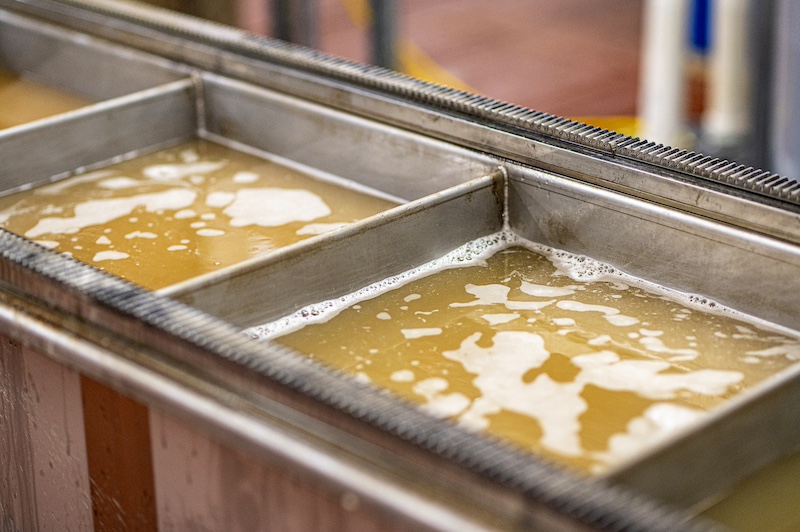
The dirty baths of the Kiwi Scour after a load has gone through.
That’s pretty much it, scaled up to hundreds and hundreds of pounds of fleeces waiting on towering shelves around the periphery of the warehouse room.
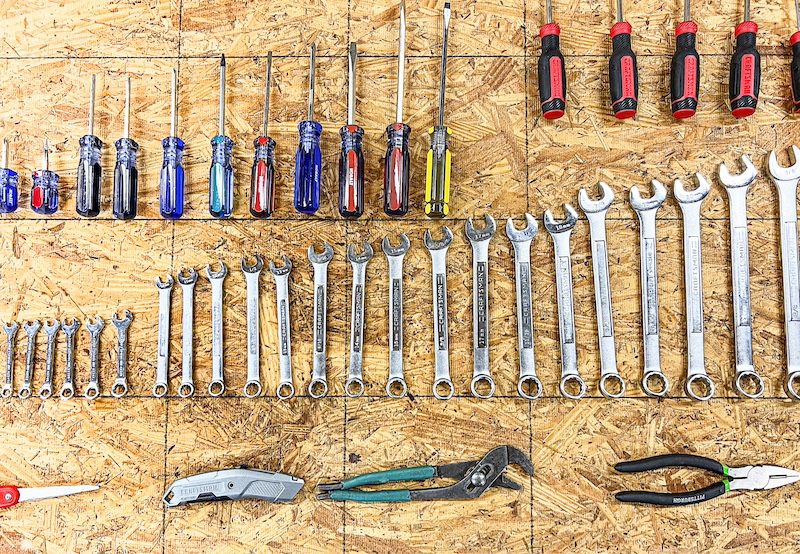
The Kiwi Scour machine is from New Zealand, and is impressively efficient. On the other hand,there’s no such thing as timely tech support from the other side of the world—so Norah has her tools arrayed and ready.
What’s ahead? Funding received from a grant by Empire State Development to the New York Fashion Innovation Center, a consortium that Hudson Valley Textile Project helped to found, will be used to expand Clean Fleece’s operation.
They plan to add lanolin recovery, add a wool storage/warehouse area, and develop a fabric finishing system to support small weaving studios and brands in the area.
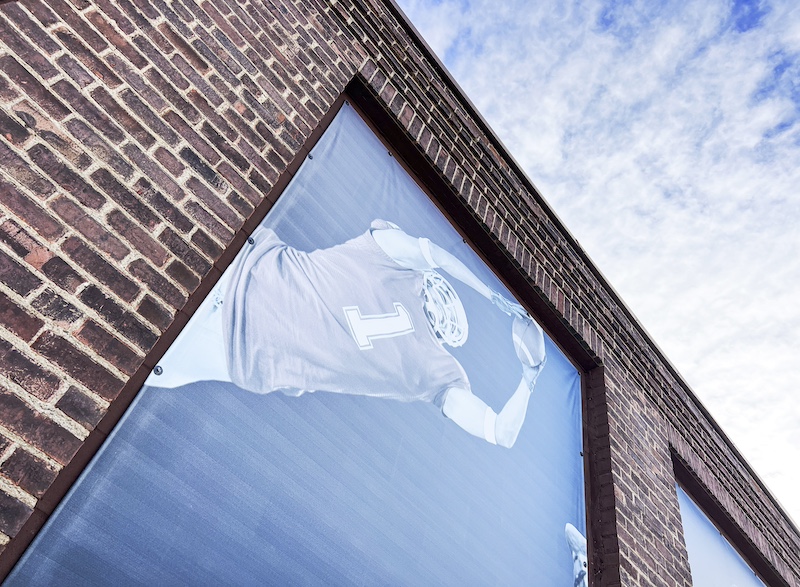
Thank you, what a great story of cooperation.
And a wonderful view of wool processing.
Norah rocks!
I really love these kinds of articles! This one was especially informative! I always feel just a little closer to understanding how much work is involved in getting that wool into my hands. My appreciation for the people involved in all the processes and those who write so beautifully about them continues to grow! Thanks to all!
So interesting. I am a hand spinner and have prepared my fleeces myself – a process so satisfying. I was wondering about the water recovery after the fleece is scoured I know first hand how dirty that water is- curious if it is recycled. Thank you for a good read!! And best of luck and success to them!
Couldn’t have said it better! Love these kinds of stories of individuals coming together to solve problems especially helping small operations.
Cheers to all! Need was identified and steps taken to solve the problem. And looking to the future to make it even better – lanolin recovery etc. It’s heartening to hear of people working together, figuring out a way, getting the necessary support and seeing success.
I love how women are so adept at identifying the need and creating the best solution that serves the highest good. Thank you for sharing such a great story. The inclusivity, support for the farmers, and cooperation is simply wonderful
I loved reading about this project. AND the pictures. I love that people are making this happen with such dedication.
Great article! I loved the twin focus on the cleaning process and the process of developing a much needed facility for small farmers. Several times over the years it has been my pleasure to help skirt fleeces at a friend’s farm on shearing day and I’ve learned from her the challenges involved in further processing. This is no small feat and it’s the first step to all that beauty on the walls and in the bins of our favorite yarn shops.
I worked for a few years at a small local mill, mostly in charge of scouring. I never got tired of watching the fleeces go from greasy dirty to fluffy clean! Like magic.
Oh! I just realized that I’m staying very close to Battenkill, and had planned to arrange a visit in the next few weeks if possible.
I’ll plan a visit to Cornwall while I’m still in the area.
Thanks so much, Gale, your stories and photos are always beautiful and inspiring.
Biggest thanks to you all. From your earlier article about a mini mill in Iceland to this one with info about Fibreshed cooperation & needs to be filled in the regional and larger North American Markets, you are helping me so so so SO much! That’s enough hinting for now, but big credit to MDK for all the assisting info!! (( Hearts ))
What an amazing process!! I now have a greater appreciation for the wool I craft with. Would love to see this up close and in person!
Oh, come on! Tell me that hero image isn’t a little pocket dog getting a bath.
Now I see it too! I can’t UN see it!
Modern Daily Dog Grooming! PIVOT!
Thank you for your article and the wonderful photos. Good, clean (!), informative reading! More power to the Hudson Valley Textile Project and the people like them.
The first photo of Norah seriously looked like she was holding a fuzzy dog!
Bravo for having a vision for a sustainable and long term vision for this beautiful natural fiber! Let’s bring back our wool industry!
What a wonderful story. From field to needles, the knowledge and skill revealed in this article and at every step of a knitted project never ceases to amaze.
I loved this trip into the world of scour!! Thank you!
There is something heroic about this small band of women performing this much needed and but not particularly glamorous work. Thanks, Gale!
Joining the chorus to say thank you, Gail and MDK, for a wonderful glimpse behind the scenes. I really enjoyed everything about this article. (Also can’t help but wonder what a whole building of wet wool smells like…..)
Fascinating article, wonderful photos! An inside peek at an amazing process. Thanks Gale!
LOVE this! My endorphins are soaring! Thanks for the Grandma Moses info.
What a fascinating process. And so thankful there are folks so passionate about our little “hobby” to make this all work. Would love to take a tour sometime. Thanks for telling (and showing) us all about it, Gale!
Interesting insight into this operation and journey of the formation of the non- profit.
So glad to know this is there. I would love to visit the Hudson valley
This is so great! As an animal lover with a few sheep/goats, it’s alway challenging for me to find mills who process small batches. Within the larger textile industry, scouring has been a bottleneck for years. Very happy to hear about this new facility.
That was a fascinating article. Thanks so much for enlightening me.
Cool story about wool fibers being cleaned and processed for home growers in the Hudson Valley area. It is astounding how hard it is to utilize this process when required poundage is so high before companies will accept the raw wool.
I once stored raw wool fibers from my sister-in-laws sheep, in heavy plastic bags in my shed for years before I found a place to have it cleaned and batted.
Frankenmuth, MI finally took on my 16 pounds – it made enough batting to make 5 quilts worth – beautifully finished off with cotton gauze mesh coverings as well.
Thanks for sharing this heartfelt story.
Cool story about wool fibers being cleaned and processed for home growers in the Hudson Valley area. It is astounding how hard it is to utilize this process when required poundage is so high before companies will accept the raw wool.
I once stored raw wool fibers from my sister-in-laws sheep, in heavy plastic bags in my shed for years before I found a place to have it cleaned and batted.
Frankenmuth, MI finally took on my 16 pounds – it made enough batting to make 5 quilts worth – beautifully finished off with cotton gauze mesh coverings as well.
Thanks for sharing this heartfelt story.
Thank you for this article! Supporting small farms and businesses is vital to our world. Learning about Clean Fleece brought joy to my soul!
Now I want to get to upstate NY and see this all! Your article is a reminder of how much work goes into the beautiful yarn we knit with.
This was fascinating for someone who sees yarn only in its final form. Who knew? Thanks so much. I can only echo other commenters in my appreciation of the people who see a need and figure out a way to solve it
Yay!
Wow! Great article, Cornwall Yarn Shop is my local shop and Gail is a great person and such a knowledgeable knitter. So nice to see The Hudson Valley Textile Project featured in this article.
Thank you for a great article. The need and cooperative aspect must certainly be appreciated by all of the fiber producers that need this process. I live in Montana and I know from locals that such businesses are few and far between for processing of wool, even places that process alpaca fiber.
Thank you for sharing this wonderful story. Wishing them all the best and love that they are helping out the ‘little’ guy so-to-speak in getting the fleeces to yarn! Wonderful to support companies like this.
Excellent and inspirational article! Thanks for such a wide range of fascinating content.
Just the feel good story I needed! I’ll be they could monetize the scouring process on YouTube — my husband can’t get enough of the filthy to clean car and gungy, forgotten cast iron to clean vids!
This story just makes me so darned happy! Everything about it. The original idea, the development of a service to meet a need, the successful growth of the enterprise. Even the excellent picture of the tools. It’s just a great story. And as a goatherd with bag upon bag of raw cashmere piled up in my tiny house, this gives me hope for one day reading a similar story about folks cleaning – and spinning – cashmere.
This is amazing!!! I live in the area and am so excited to think of the area being a hub for fiber businesses!
Thank you for the article! Fascinating. Can’t wait to hear about the lanolin recovery – that is so much better than letting it go into the water system.
Thank you so much for all the hard work it has taken to make this happen!!
Thank you for this amazing article! I feel so lucky to be a Hudson Valley native. There is so much fiber joy to be had around here! I had Shetland sheep for about ten years. I used to go to a mill in Red Hook, and after that closed a new one in Hillsdale. I have a few fleeces still in my garage waiting for something, and it’s wonderful to know about this option.